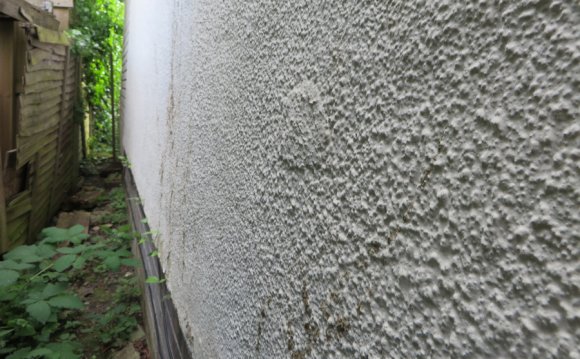
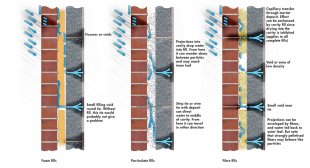
The Problem
Cavity walls were first introduced as a measure against water ingress in the 1890’s and slowly became the accepted norm over the next few decades. The outer leaf, which can be water permeable, acts to block, but will not always stop wind-driven rain from penetrating. A cavity behind the outer leaf allows any water that penetrates to drain down the cavity face of the outer leaf and pass safely to the outside.In the late 1970s, the need for energy conservation made the cavity a convenient location to place various types of insulation materials, commonly polystyrene beads, and mineral wool insulation. Now all new build cavity walls contain insulation and many millions of homes with walls that originally were built with empty cavities have had insulation retrofitted
Since the initial introduction of retrofit cavity wall insulation solutions have been developed and improved and the use of some materials has been restricted to areas of lower exposure to wind driven rain. Test regimes such as those required for BBA certification ensure that systems are able to resist the penetration of liquid water. In all exposure conditions through the insulation from the outer to inner leaf of masonry. Installation is completed by trained installers and in line with the system instructions. BBA Certificates exist for systems using mineral wool, polystyrene bead insulation and polyurethane foam. A condition of these certificates is that manufacturer’s instructions require an assessment of the condition of the outer leaf to be made and the cavity itself does not have significant debris or mortar projections and that the masonry, especially the pointing and mortar beds, are in a good state of repair at the time of installation. Most system are also guaranteed to prevent the passage of liquid water for a period of 25 years and this also requires that the masonry is kept in good condition.
That said problems of damp penetration can occasionally occur. Most commonly these pertain to the state of repair of the wall or the cavity debris has not been noticed. In these circumstances a heavy rain event could place stresses in terms of volumes and intensity of water on the insulation system that are beyond those tested for during certification and result in damp penetrating into the building’s interior causing condensation, mould growth and damage to decoration. Clearly in these circumstances reducing the amount of water penetrating the outer leaf will reduce the stress on the insulation system in the event of a similar rain event.